SIDEFFECT – Development of a dynamic induction welding process for the aeronautic industry
The lightening of structure represents a strategic issue for the aeronautic industry. This industry is called upon to reduce its environmental impact while controlling costs.
Indeed thermoplastic composites are a major asset to substitute metal materials. They provide true advantages thank to ther intrinsic properties :
- Mechanical performances
- Resistance to mechanical agents
- Recycling performances
- Industrial perspective for assembly line automation
Nevetheless the cost-performance ratio of composite fuselage panel assembly operations (blocking, drilling, riveting) are an obstacle to become as competitve as metallic fuselage panel assembly operations.
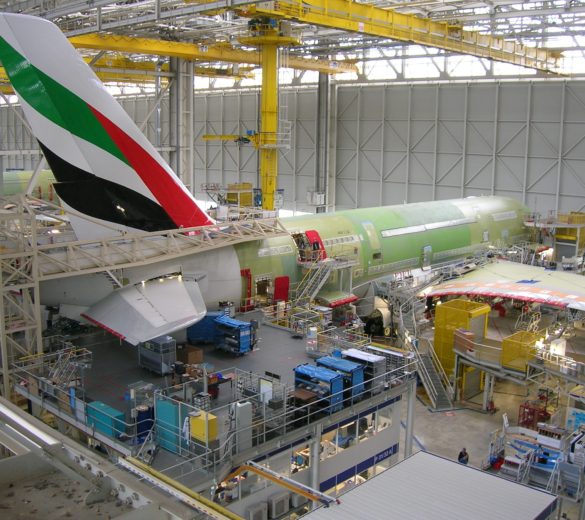
The SIDEFFECT project aims to answer this problematic. That’s why EUROPE TECHNLOGIES, provider of innovative industrial solution for the aeronautic, has worked with IRT JULES VERNES and its partners to develop an automated assembly process wihtout drilland or fastenings to increase the production rate and reduce composite fuselage panel assembly operations costs.
This project follows on from SOFUSIN project. It aimed to get necessary know-how on the induction weld process of composite components with thermoplastic matrix.
SIDEFFECT
The project aim was to manufacture by the mean of an automatic induction welding process a plane fuselage panel. The major axis took into account were :
– lightning protection
– complexe geometry of aero structure parts
– cost/performance factor
The project has been realized trough the following tasks :
- Define, design and realise a dynamic welding cell at R&D and pilot scale
- Define elementary rules of design, means, processes and products
- Design and manufacture of the mock-up assembly tooling
- Process demonstration on a representative mock-up of a self-hardened fuselage panel
- Setting of a fisrt level of electrothermal modelling
- Material health analysis of welded parts
- Mechanical tests of welded parts
Our expertise
Taking part in the project made possible for Europe Technologies to complete its know-how for welding processes (ultrasonic, laser, spin, hot-plate, infrared) thanks to the key parameters identification, the know-how capitalization regarding the constraints and limits of the processes and showing our capacity to integrate new process.
Europe Technologies and its brands SONIMAT, ORATECH and GEBE2 gathered their respective expertises and means : engineering office (mechanical, automatisation), composite and metal machining, programming, robotic and R&D.
For the design and manufacturing of the R&D robotised cell, ORATECH and SONIMAT designed and manufactured the weld effector aiming to heat the parts to be assembled and press against each other.
ORATECH designed and manufactured an assembly tooling.
GEBE2, SONIMAT and the technical center developped, installed and set up the automatisation and programming of the cell.
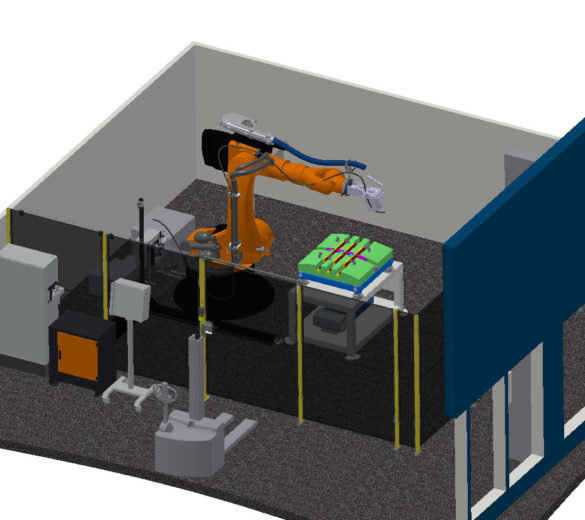
This integrated industrial approach made possible to provide to our clients turnkey welding solutions adaptated to their needs.
Induction welding process
How does it work ?
The induction welding process principle is to create an electromagnetic field around the components that are to be assembled. This electromagnetic field will be captured by the carbon fiber of parts and the tempearature will rise. Finally a pressure will be applied on parts to create a contact and controlled cool down, to weld parts together.
Advantages
- Low electric consumption
- Additionnal material not required (no fouling of the tooling)
- Low maintenance
- Quick welding
- Precise welding
- Small area to be heated on the part
- Hard-to reach-areas welding
- Automatisation of the welding process (easy to set up, repetitive process)
PARTNERS
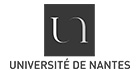
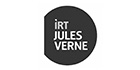
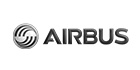
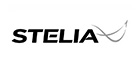
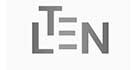
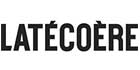
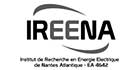
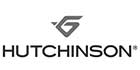

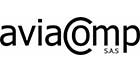